1.什么是熱等靜壓?
HIP是Hot Isostatic Pressing的縮寫,是以高溫高壓氣體為壓力傳熱介質(zhì)(數(shù)百~2000℃,等靜壓數(shù)十~200MPa),對(duì)目標(biāo)材料進(jìn)行各向同性壓縮壓實(shí)技術(shù)。 )。氬氣是最常用的壓力介質(zhì)。
1950年代在美國(guó)發(fā)明,用于金屬、硬質(zhì)合金、陶瓷等各種材料的成型、燒結(jié)、接合和缺陷去除。
圖1為外觀,圖2為HIP設(shè)備的配置。
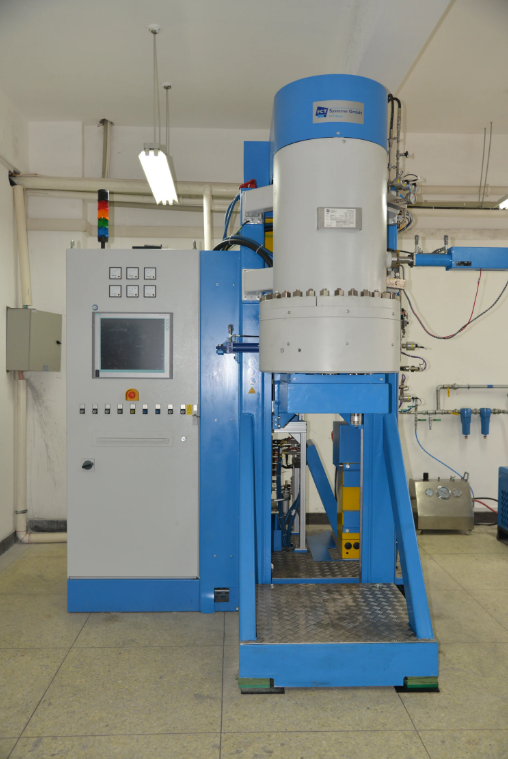
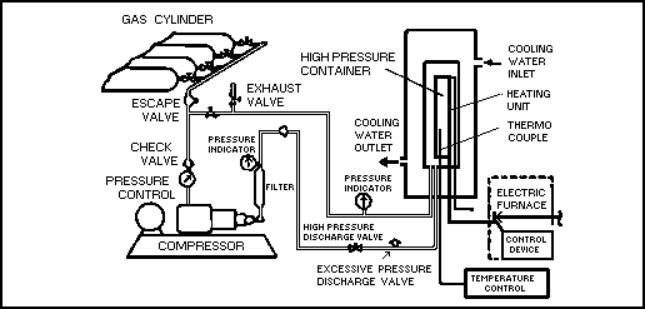
2.臀壓與熱壓的區(qū)別
熱壓與臀部非常相似。銑削、鍛造和擠壓也適用于高溫高壓,但與熱等靜壓不同的是,它們不適用于等靜壓。
髖壓與熱壓最明顯的區(qū)別是髖壓是利用氣壓對(duì)材料施加等靜壓,而熱壓只施加單軸壓力。
與熱壓相比,臀部可以提供與壓制后的初始形狀相差不大的材料形狀。即使改變形狀后,材料也能保持原來(lái)的形狀,受產(chǎn)品加工的限制相對(duì)較少。通過(guò)充分利用這些特點(diǎn),髖關(guān)節(jié)已被應(yīng)用于各個(gè)領(lǐng)域。
為了清楚地解釋熱等靜壓和熱壓之間的區(qū)別,我們假設(shè)熱等靜壓或熱壓分別應(yīng)用于材料a(內(nèi)部有孔的金屬)和材料B(端部不平整的金屬)。
如圖 3 所示,如果采用 hip 技術(shù),材料 a 會(huì)收縮并保持其初始形狀,直到內(nèi)部孔隙消失并因擴(kuò)散作用而結(jié)合。并且材料B根本不會(huì)改變它的形狀,因?yàn)榫鶆虻膲毫κ┘釉诓黄教沟倪吘壣稀?/p>
如圖4所示,在熱壓的情況下,材料a會(huì)出現(xiàn)與臀部相同的現(xiàn)象。材料B不能保持其初始的不均勻形狀,因?yàn)閴毫H施加在凸部上。材料 A 和材料 B 在熱壓后的最終形狀會(huì)有所不同,這取決于所使用的模具和沖頭的形狀。應(yīng)用熱壓技術(shù)制造大型制品和成型零件,是由于與模具的摩擦造成的不均勻性以及變形過(guò)程中溫度和尺寸的限制。
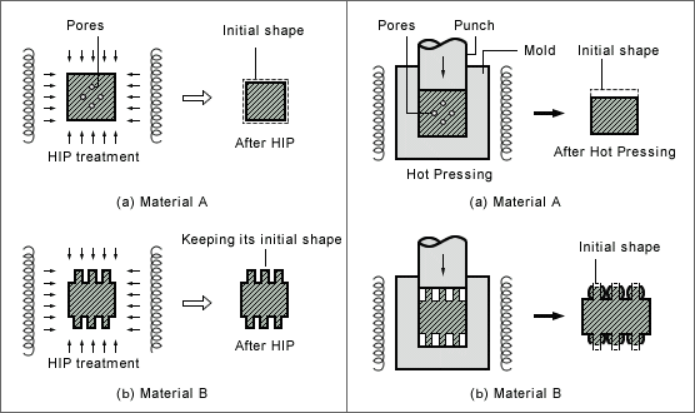
3.臀部應(yīng)用模式
材料需要根據(jù)情況進(jìn)行處理。最典型的方法包括“膠囊法”和“無(wú)膠囊法”。
如右圖所示,“膠囊法”是將粉末或由粉末成型的主體密封在密封膠囊中,并在臀部前排空膠囊。
這種“膠囊法”即使對(duì)于普通燒結(jié)技術(shù)難以燒結(jié)的材料也能提供高密度。因此,它最常用于粉末材料的加壓燒結(jié)工藝。也用于不同類型材料的擴(kuò)散結(jié)合或高壓浸漬碳化。
下表總結(jié)了無(wú)囊法的主要材料和髖關(guān)節(jié)治療溫度/壓力。
如果材料中的氣孔是孤立的、封閉的,并且不與材料表面相連,這些氣孔可能會(huì)被臀部處理擠壓和消除。另一方面,即使經(jīng)過(guò)臀部處理,與材料表面相連的開(kāi)口也不會(huì)受到擠壓。因此,對(duì)具有封閉孔的材料進(jìn)行臀部處理可以提供整個(gè)材料的高密度。
這種材料髖關(guān)節(jié)不需要膠囊,稱為“無(wú)膠囊法”。用于去除燒結(jié)件上的殘余氣孔,去除鑄件內(nèi)部缺陷,修復(fù)因疲勞或蠕變而損壞的零件。
4.HIP具體應(yīng)用
髖關(guān)節(jié)廣泛應(yīng)用于以下領(lǐng)域:
(1)粉末的加壓燒結(jié)
(2) 不同類型材料的擴(kuò)散鍵合
(3)去除燒結(jié)件中的殘余氣孔
(4)鑄件內(nèi)部缺陷的去除
(5) 修復(fù)疲勞或蠕變損壞零件
(6)高壓浸漬碳化法
我們以硬質(zhì)合金的生產(chǎn)作為應(yīng)用髖關(guān)節(jié)技術(shù)的具體例子。
硬質(zhì)合金在韌性上不如鋼和其他金屬,而且很容易出現(xiàn)粗大顆粒和氣孔等缺陷。為了充分利用這些材料的天然特性,就需要去除這些內(nèi)部缺陷,而臀部是消除這些缺陷的最有效手段。
由于在燒結(jié)硬質(zhì)合金時(shí)使用鈷等金屬的液相作為粘結(jié)相,因此可以將普通燒結(jié)體壓實(shí)到接近理論密度的密度。但燒結(jié)體內(nèi)部仍有細(xì)小氣孔,對(duì)硬質(zhì)合金起致命作用,在正常情況下可承受的壓力下斷裂。熱等靜壓的目的是完全消除燒結(jié)體中的一些氣孔。
表1為熱等靜壓下力學(xué)性能的變化,圖3為熱等靜壓前后彎曲強(qiáng)度的威布爾圖。
表1 HIP處理對(duì)硬質(zhì)合金力學(xué)性能的影響
髖關(guān)節(jié)置換術(shù)之前 | 髖關(guān)節(jié)置換術(shù)后 | |
相對(duì)密度 [%] | 近 100 | 近 100 |
硬度 [HRA] | 91.0 | 91.0 |
抗彎強(qiáng)度[Mpa] | 2450 | 2940 |
斷裂韌性 [Mpa·m1/2] | 10 | 10.5 |
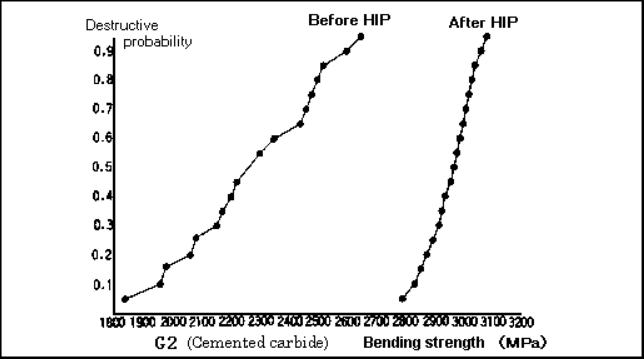
如上圖所示,HIP處理不會(huì)改變硬質(zhì)合金的密度和硬度。然而,通過(guò)去除細(xì)孔,彎曲強(qiáng)度大大提高,強(qiáng)度的偏差變得非常小,從而提高了可靠性。
OU ON PEUT TRUVER LES REFERENCES DE CET INFORMATIONS MERCIII
您好,
感謝您對(duì)我們的博文發(fā)表評(píng)論。
如果您有任何問(wèn)題,您可以給我們發(fā)電子郵件至 [email protected].
此致,
美特優(yōu)硬質(zhì)合金