Simple classification of lathe tools
Based on the type of workpiece surface being machined
Lathe tools can be categorized into outer circular turning tools, internal bore turning tools, and end-face turning tools.
Outer circular turning tool
The outer cylindrical turning tool is used for external turning, processing the outer cylindrical surface of the workpiece to achieve the required dimensions, geometric tolerances, and surface quality, as shown in Figure 1.

Internal bore turning tool.
The internal bore turning tool is used for internal turning, as shown in Figure 3-2. It is a method of enlarging the inner bore of a workpiece or machining the inner surface of a hollow workpiece using turning techniques. Most of the external turning processes can be used for turning the internal bore. In this case, the tool is stationary (rotating in the opposite direction to the boring tool in machining centers).
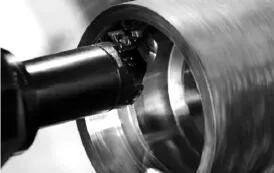
End-face turning tool
The end-face turning tool is used for end-face turning, as shown in Figure 3. The tool tip always lies on a line intersecting with the spindle axis at a certain point, resulting in a plane or conical surface passing through that point and perpendicular to the spindle axis. End-face turning tools refer to tools whose primary cutting edge is capable of cutting the end face of the workpiece.
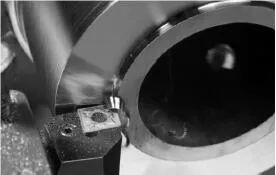
According to the tool structure
Solid turning tool
The solid turning tool, as shown in Figure 4?is characterized by having both the working portion and the shank made from the same material, in contrast to welding tools or indexable tools with non-detachable inserts. Typically, solid turning tools are made from materials such as high-speed steel or high-performance high-speed steel. These tools offer excellent rigidity, and operators can grind the cutting portion into flat surfaces, inclined surfaces, and various shaped surfaces according to the machining requirements.
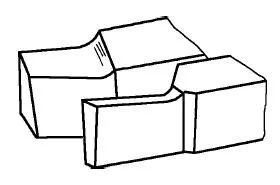
Welded turning tool.
The welded turning tool, as shown in Figure 5, is created by machining a tool groove on a steel tool shank according to the geometric angles of the turning tool. High-speed steel or hard alloy blades are then welded inside the tool groove using welding material. After grinding to the selected geometric parameters, the tool is used for turning. Due to the widespread use of CNC lathes and multi-axis machining centers, and the disadvantages of welded turning tools, such as the tendency to develop microcracks and reduced performance in hard alloys after welding, they are now rarely used.
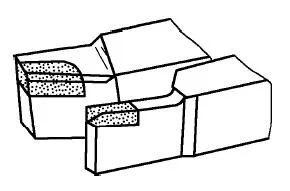
Collet chuck turning tool
The collet chuck turning tool, as shown in Figure 6, utilizes standard hard alloy welded inserts that are mechanically clamped onto the tool shank for use as turning tools.
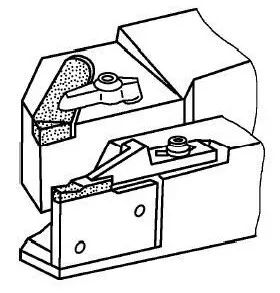
Indexable turning tool
The indexable turning tool, as shown in Figure 7, is a collet chuck turning tool that uses indexable inserts. When one cutting edge becomes dull, it can be quickly indexed to the next adjacent cutting edge, allowing the tool to continue working until all the cutting edges on the insert are dull. Only after all the cutting edges on the insert have become dull is the insert discarded and recycled. After replacing it with a new insert, the turning tool can resume its operation.
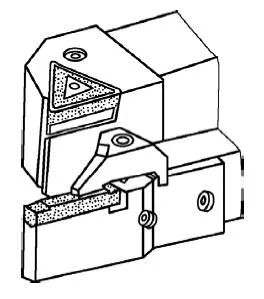
Principles for selecting lathe tool geometry parameters
1.80-degree rhombic inserts are suitable for a wide range of applications, from rough machining to finishing. Additionally, their long cutting edges allow for double-sided positioning, providing high clamping strength and facilitating interrupted cutting and heavy machining. For contour machining, 55-degree or 35-degree rhombic inserts are typically used.
2.The larger the insert nose angle, the higher the cutting edge strength, which is advantageous for interrupted cutting but may be limited by the workpiece geometry. Using triangular inserts with an included angle of 82 degrees in the form of an unequal-sided and unequal-angled hexagon can compensate for this limitation.
3.When using a minimal back cutting depth, even an equilateral unequal-angled hexagonal (80-degree) insert that ensures cutting edge strength can be highly effective.
4.Circular inserts provide the highest strength and are best suited for applications requiring excellent surface finish. However, it’s important to note that circular inserts may experience vibrations when machining slender or thin-walled workpieces, and managing insert changes can be more challenging.
5.Large-sized and thick inserts, or inserts with a vertical orientation, offer greater clamping strength and are suitable for heavy machining.
6.When using negative-rake inserts, square inserts are the most economical choice because they have four edges on one side and eight edges when both sides are utilized. They also have a high-strength 90-degree nose angle. The next best option is triangular inserts with three edges on one side and six edges when both sides are used.
7.The nose radius of an insert refers to the size of the circular arc at the insert’s tip. A larger nose radius results in higher machining accuracy and insert strength, but it can increase radial cutting forces, leading to vibrations and challenging chip management.
8.The typical range for nose radius is 0.4 to 1.2 mm. However, for heavy machining, it’s advisable to select a larger nose radius for better insert strength, while for finishing operations, a smaller nose radius is preferred from a cutting edge strength perspective.
?
Illustration for the selection of tool insert shapes
Equilateral triangular inserts can be used for outer circular turning, end-face turning, and internal bore turning with a primary included angle of 60° or 90°. However, due to their smaller nose angle, lower strength, and reduced durability, these inserts are suitable for light cutting applications.
Square inserts have a nose angle of 90°, which is larger than the 60° nose angle of equilateral triangular inserts. Consequently, square inserts exhibit improved strength and heat dissipation properties. They are versatile and mainly used for outer circular turning, end-face turning, and boring with primary included angles of 45°, 60°, 75°, and others.
Pentagonal inserts have a nose angle of 108°, offering high strength, durability, and a large heat dissipation area. However, they generate significant radial forces during cutting and are best suited for applications with good machining system rigidity.
Rhombic inserts and circular inserts are primarily employed for machining formed and curved surfaces.