Reducing CO2 greenhouse gas emissions has become the goal of the world, and now many places are discussing to levy CO2 emission tax. Due to the emergence of new fields, and people have to adapt to the existing fields, the above requirements also have a considerable impact on the research and development of machining tools. This is because more than ever, there is a need to replace drives, update lighter materials, and save energy and resources. R & D personnel see great potential for design modifications to tools, new coatings, new machining strategies, and digital solutions that respond in real time to a variety of conditions within the existing framework.
The current trend is to use these materials in new light aluminum lithium alloys, which will soon overwhelm traditional cutting tools and occupy an absolute advantage. Therefore, the demand for special high-performance tools for such applications will continue to increase. For example, aircraft parts made of aluminum alloy are usually processed up to 90%. According to the required part geometry, many grooves and cavities need to be milled out of the metal to ensure stability and reduce weight. In order to produce high quality parts economically and efficiently, high speed cutting (HSC) is needed to process the parts, and the cutting speed can reach up to 3 ? 000 ? M / min. Too low cutting parameters will lead to chip accretion, which will lead to rapid wear and frequent tool change. Because of the long running time of the machine tool, the cost is high. Therefore, machine tool operators specializing in aluminum processing have good reasons to require their cutting tools to obtain cutting data and tool life above the average level, as well as extremely high machining reliability.
We have shown how to deal with these complex requirements. The 90 ° milling cutter is equipped with a new type of indexable blade. It uses a new PVD coating, manufactured using the “hipims method.”. Hipims stands for “high power pulsed magnetron sputtering”, a technology based on magnetron cathode sputtering. The unique feature of this physical coating process is to form a very dense and smooth PVD coating, which can reduce the friction and the tendency of chip accretion. At the same time, this method improves the stability of the cutting edge, and increases the resistance of the back face wear, thus achieving the maximum metal removal rate. Field tests have shown that hipims indexable blades have advantages over standard types. Tool life increased by 200%. The demand for high-performance cutting tools for processing aluminum alloy is growing, especially in the aviation industry and automobile industry.
Dynamic milling: a milling strategy focusing on efficiency
Many industries (especially the supply industry) are facing the pressure of improving the processing stability, accelerating the processing speed, reducing the processing cost and ensuring the processing quality. At the same time, the requirements of machining reliability and cost efficiency are also strict for surface quality and dimensional stability. In addition, the demand for lightweight or heat-resistant materials is also growing. However, due to these properties, these materials from the ISO m and ISO s material groups are often difficult to accurately process. Dynamic milling provides solutions for this field, while ensuring production efficiency and machining reliability, which is why more and more metal processing companies rely on this method.
The difference between high performance cutting (HPC) and high dynamic cutting (HDC) is the movement and force of milling cutter. In the high performance cutting process, when the milling tool moves, the cutting depth is relatively small; in the high dynamic cutting process, the CAD / cam control system controls along the path of the tool during the processing of the workpiece shape (Figure 1). This prevents or at least reduces non cutting time. Moreover, the cutting depth of high dynamic cutting is much larger than that of traditional high-performance cutting, that is, the stroke distance is reduced, because the whole tool length can be used.
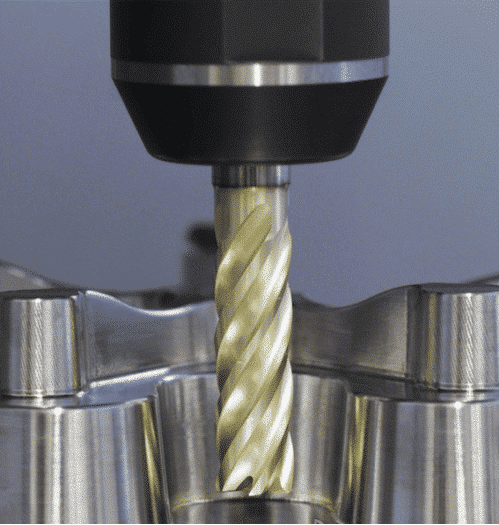
Figure 1 dynamic milling strategy requires appropriate workpiece, milling tool, machine tool and CAD / CAM system
In the process of high performance cutting, the envelope angle is often very large. Therefore, the force in the process is also very large. This will speed up the tool and machine spindle wear. On the other hand, dynamic milling is characterized by high machining stability and long tool life. Generally speaking, the envelope angle of high dynamic cutting is very small, that is to say, the force of the tool and machine tool is much smaller than that of high performance cutting. Compared with high performance cutting, high dynamic cutting has higher cutting parameters, smaller non cutting time and greater machining stability, so its metal removal rate is very high.
Adaptive feed control: using real-time parameters to optimize cutting parameters
For a long time, automation, digitization and networking technology have been widely used in many metal processing fields, and are very popular. In particular, the hardware and software used to collect and analyze real-time data have made a huge leap in performance. Software tools demonstrate how these tools provide numerous opportunities for optimizing processes (Figure 2). Adaptive feed control analyzes the input data of machine tool in real time and adjusts the machining accordingly. This answers a key question for many users. That is, how to give full play to the benefits of the machine tool without major changes to the process or complex reprogramming? The software can greatly shorten the processing time of a single piece. The software has been integrated with the existing control program, and the data in the program has been applied to the machining process.
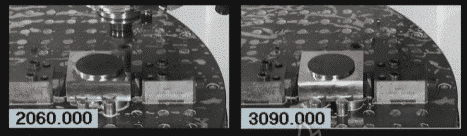
Figure 2 dynamically adjust the feed according to the cutting conditions. In this way, the production time of a single piece can be shortened and the processing reliability can be improved
During the first tool cutting, the computer “l(fā)earns” the idle output of the spindle and the maximum cutting efficiency of each tool. It then measures the spindle output up to 500 times per second and automatically adjusts the feed in each case. That is to say, the machine tool always runs with the maximum feed amount of each tool. If the cutting conditions change (cutting depth, machining allowance, wear, etc.), the computer will adjust the speed and output in real time. This not only has a positive impact on the machining time of the workpiece, but also improves the machining reliability with the optimized milling characteristics. The force acting on the spindle is more constant, and the service life of the cutter is prolonged.
If there is a risk of cutter breakage, the computer will immediately reduce the amount of feed or stop the operation completely. Using our high-end computer processing customers, its processing efficiency has achieved amazing improvement. If the process is compatible, the processing time can be reduced by 10%. We have managed to cut the processing time by another half. When the number is large, it will free up a lot of machining capacity. ” In addition, this method is effective no matter whether Walter tool is used or not. It only needs to meet the system requirements of the machine tool.