?Names of the Various Parts of an End Mill
Names of the various parts of an end mill:
Structural Types of End Mills
Classified by the Number of Cutting Edges:
The cylindrical surface and end face of an m?yn końcowy usually have cutting edges distributed on them, which can engage in cutting simultaneously or individually. Based on the number of blades, end mills can be categorized into double-edge, triple-edge, quadruple-edge, and multi-edge types.
The fewer the number of blades, the larger the chip flute, but the worse the rigidity.
Comparison of the advantages and disadvantages of end mills with different numbers of blades:
According to the type of bottom end tooth shape
According to the shape of the cutting edge
General-purpose end mill
Widely used, applicable to slot machining, side machining, and step surface machining, etc. In addition, it can be used in all situations of rough machining, semi-finishing, and finishing.
Tapered end mill
Used for conical surface machining after general cutting, such as mold draft angle machining and concave portion machining, etc.
Gear-type end mill
The cutting edge is wavy, producing fine chips, with low cutting force, suitable for rough machining, not suitable for finish machining.
Forming end mill
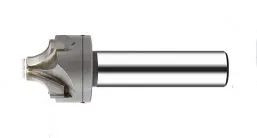
A forming blade is a cutting edge that is shaped to match the contours of the workpiece being machined. Special shapes typically need to be custom-made based on the product’s shape and dimensions.
According to the blade arrangement of end mills


By tool material
End mills can be classified by material into: high-speed steel, solid carbide, carbide with coating, CNB, PCD, etc.
?
Key Points for Selecting End Mills
When using an end mill, multiple factors need to be considered to ensure machining efficiency, precision, and tool life. Here are some key considerations:
① Material of the workpiece: Different materials (such as steel, cast iron, aluminum alloy, plastic, composite materials, etc.) require tools with different characteristics. For example, when machining aluminum alloy, a specialized aluminum end mill can be chosen, which typically has good chip evacuation and heat resistance; when machining high-hardness materials, a carbide tool with a high-wear-resistant coating should be selected.
② Machining form and precision requirements: Choose the shape and number of cutting edges based on the shape of the machining surface (plane, slot, contour, etc.) and the required surface roughness. For instance, a ball nose end mill is suitable for complex surface machining, while a flat or rounded end mill is suitable for plane and edge machining. For high-precision machining, choose an end mill with higher arc precision.
③ Helix angle of the end mill: The helix angle affects cutting efficiency and tool life. When machining materials with poor thermal conductivity (such as stainless steel), a large helix angle can improve chip evacuation and heat dissipation, extending tool life. For thin-walled workpieces or machining with poor rigidity, a small helix angle can reduce cutting forces and avoid workpiece deformation.

④ Tool material and coating: Carbide is the most commonly used tool material. For different working conditions, selecting the appropriate carbide grade and coating (such as TiCN, TiAlN, etc.) can enhance tool performance. High-speed steel (HSS) is suitable for low-speed and low-hardness material machining, while carbide is more suitable for high-speed and high-hardness material machining.
⑤ Tool structure: Solid, brazed, and indexable tools each have their advantages. Solid tools have good rigidity and are suitable for precision machining; brazed and indexable tools are convenient for blade replacement and are suitable for mass production.
⑥ Number of flutes and shank structure: The number of flutes affects the tool rigidity and chip flute size. When the workpiece rigidity is low, it is advisable to choose a tool with fewer flutes to improve chip evacuation; the shank design (standard, long neck, tapered neck) needs to be selected based on the machining depth and workpiece shape. Tapered neck end mills provide better rigidity and machining accuracy.

⑦ Tool length: Under the condition of meeting the machining requirements, choose the shortest tool length as much as possible to increase stability, reduce vibration, and thereby improve the quality of machining.
⑧ Cost-effectiveness: Consider the tool cost and machining efficiency comprehensively and choose a cost-effective solution.
In summary, the selection of end mills is a process of comprehensive consideration, involving workpiece material, machining requirements, tool performance, cost-effectiveness, and other aspects. Correct selection can greatly improve machining efficiency, reduce costs, and ensure machining quality.