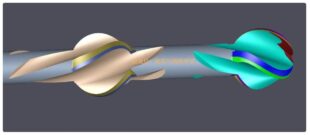
The lollipop end mill (also known as an arched ??? or T – type ball – nose end mill) is a specially designed milling cutter. It gets its name from its appearance, which looks like a lollipop as a whole. It consists of two parts: a shank and a cutter head. The shank is usually cylindrical, which is convenient for being installed on the spindle of a machine tool. The cutter head is a spherical or approximately spherical cutting part, just like the candy ball of a lollipop, and the neck connecting the shank and the cutter head is relatively thin, just like the stick of a lollipop. This structural design enables the cutter to go deep into complex areas such as deep cavities and narrow grooves of workpieces for processing. The following is an analysis of its detailed use scenarios, application scope, advantages, applicable working conditions and processing materials:
Usage Scenarios and Application Scope
The lollipop end mill is mainly used in the following machining scenarios:
Undercut machining: Such as areas that are difficult for ordinary end mills to reach, like mold cavities, turbine blades, and inner arc runners.
Deep – cavity machining: Suitable for machining the inner walls of deep grooves or holes with a relatively large length – diameter ratio, such as aviation structural parts, hydraulic valve blocks, etc.
Deburring: Especially suitable for removing burrs on the inner walls of holes, particularly for internal deburring of parts with complex shapes.
Precision finishing of steep walls: Can be used for 2.5 – axis machining of cavities, bosses, and corners to improve surface finish.
Hole – expanding machining: The patented lollipop hole – expanding end mill of Suzhou Shande Precision Tools can simplify the traditional hole – expanding process that requires switching multiple cutters, and improve efficiency.
Main Advantages
Compared with traditional milling cutters, lollipop milling cutters have the following advantages:
Special geometric design: The ball – nose shape can access areas that are difficult for ordinary milling cutters to reach, such as undercuts, deep cavities, etc.
Efficient chip removal: Optimized chip pocket design and spiral heat dissipation reduce built – up edges and the risk of tool breakage.
High surface quality: Edge ?treatment (passivated edge treatment) reduces cutting resistance and improves the finish of workpieces.
Long tool life: Made of cemented carbide materials (such as tungsten steel) and with coating technology, it has stronger wear resistance.
Reduce tool change times: Can complete rough machining and semi – finishing machining at the same time, improving machining efficiency.
Applicable Working Conditions
Lollipop end mills are suitable for the following machining conditions:
Numerical control (NC) machine tools (CNC machining centers, engraving machines, precision engraving machines): Suitable for the machining of high – precision and complex curved surfaces.
Machining with large overhangs: The long – neck design (such as a neck length of 40 mm) is suitable for deep – cavity machining and reduces tool vibration.
Small – batch or customized production: Non – standard tools can be customized and are suitable for the machining of special workpieces.
Difficult – to – machine materials: Such as superalloys, titanium alloys, stainless steels, etc., reducing the accumulation of cutting heat.
Suitable Materials for Machining
Lollipop end mills can machine a variety of materials, including:
Steels: Carbon steel, die steel (such as P20, H13), high-speed steel, stainless steel (such as Cr13).
Cast iron: such as HT200, HT300, etc.
Non-ferrous metals: aluminum, copper, aluminum alloys, etc. However, special aluminum end mills should be selected to avoid tool sticking.
Difficult-to-machine materials: titanium alloys (such as TC4), superalloys (such as Inconel 718).
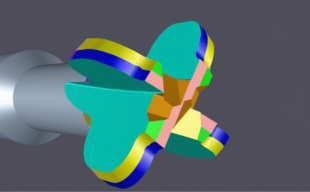
How to Select the Appropriate Lollipop End Mill
Based on Machining Feature Parameters
The machining features of the workpiece (such as cavity depth, fillet radius, and surface complexity) are the core basis for selection:
Cavity depth and neck length
When machining deep cavities or narrow grooves (such as deep grooves in molds), focus on the tool’s neck length. The neck should be 5 – 10mm longer than the cavity depth to ensure the cutter head can fully contact the machining area while avoiding interference between the neck and the cavity wall. However, an excessively long neck will reduce rigidity and easily cause vibration. Therefore, for deep cavity machining, it is recommended to choose tools with a thickened neck or made of integral cemented carbide to improve stability.
Fillet radius and cutter head diameter
The spherical radius of the lollipop end mill’s cutter head must match the fillet radius of the workpiece. For example, when machining a fillet of R5mm, a tool with a ball head radius of 5mm should be selected. If the radius is too small, it will increase the number of tool passes; if it is too large, precise forming cannot be achieved. For complex curved surfaces, it is advisable to use a combination of cutter heads of multiple specifications. Large – diameter cutter heads are used for rough machining to efficiently remove allowances, and small – diameter cutter heads are used for finishing to ensure detailed accuracy.
Surface steepness
When machining steep curved surfaces (such as the vertical side walls of mold cavities), the cutting angle range of the tool needs to be considered. The cutting edge of the spherical cutter head has a wide coverage range, but the neck design must avoid collision with the workpiece. In this case, a short – neck ball – nose end mill can be selected to reduce the risk of interference.
Based on Precision and Surface Quality Requirements
Different scenarios have significantly different requirements for machining precision (such as dimensional tolerance, form and position tolerance) and surface roughness, so targeted selection is necessary:
High – precision finishing
For example, in the mirror finishing of mold cavities, which requires a surface roughness of Ra≤0.8μm, ultra – fine grain cemented carbide or CBN (cubic boron nitride) tools should be selected. The spherical error of the cutter head must be controlled within 0.001mm, and the cutting edge must undergo precision grinding to ensure stable cutting.
General – precision rough machining
If only basic dimensional requirements need to be met (such as deep groove machining of general mechanical parts), high – speed steel or ordinary coated cemented carbide tools can be used. Priority should be given to cost – effectiveness and durability, without excessively pursuing high – precision parameters.
??
With its unique ball – head design and optimized cutting performance, the lollipop end mill performs excellently in complex machining scenarios such as deep cavities, undercuts, and deburring. Its advantages include efficient chip removal, long service life, and high surface quality. It is suitable for machining difficult – to – cut materials (such as titanium alloys and die steels) and special structures (such as deep holes and inner arc runners) on CNC machine tools. For manufacturing industries requiring high precision and efficiency (such as aerospace, mold, and automotive industries), the lollipop end mill is a highly valuable machining tool.