Modern medical appliances are in great demand, and the structure of many medical appliances is also very sophisticated and complex, so a new manufacturing technology is needed to replace the traditional production. Nowadays, metal powder metallurgy can mass produce products with complex shapes in a short period of time, which can meet the manufacturing requirements of medical appliances and become an ideal manufacturing method.
Metal powder metallurgy technology
Metal powder metallurgy is a Near Net Shape Forming process developed rapidly in the 20th century. The general process is powder + binder mixing powder metallurgy degreasing sintering.
The first is to mix the polymer with powder to produce a feeding material with sufficient fluidity, uniform mixing and satisfying injection requirements under certain conditions. The second is to select an appropriate temperature, pressure, and speed for powder metallurgy. The second is to sinter the powder after removing the binder from the injection blank. Finally, metallurgical bonding is formed, and the required parts are obtained.
Medical appliances manufactured by metal powder metallurgy technology
Medical appliances generally require good usability and long enough service life, and flexible design in structure and shape design.
Metal powder metallurgy technology was first used in medical appliances in the early 1980s and has become the fastest-growing area of metal powder metallurgy market.
Orthodontic bracket
Metal powder metallurgy technology was first used in medical treatment to produce some orthodontic appliances. These precision products are very small in size, biocompatibility and corrosion resistance. The main material used is 316L stainless steel. At present, orthodontic brackets are still the main products of metal powder metallurgy industry.
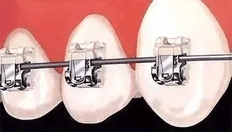
Forestadent Ltd. has produced a two-way inverted orthodontic bracket with metal powder metallurgy technology. The mechanical retention can be increased by 30%. The friction of bracket to archwire can be greatly reduced by polishing the bracket after one-time forming with metal powder metallurgy.
Surgical tools
Surgical tools require high strength, low blood contamination, and corrosive disinfection procedures. The design flexibility of metal powder metallurgy technology can meet the application of most surgical tools. It also has technological advantages and can produce various metal products at low cost. Step by step replaces the traditional production technology and becomes the main manufacturing method.
FloMet Co., Ltd. developed a kind of stainless steel claw using metal powder metallurgy technology. It is made of 17-4PH stainless steel with a density greater than 7.5g/cm3. It can be used to grasp objects in the human body during operation and has the function of tweezers. Its design is quite complex and requires high production accuracy.
Using metal powder metallurgy technology to form and sinter, it can achieve a high tolerance level and does not need a large number of follow-up processing technology to avoid damage to the linear and geometric shape of the claw.
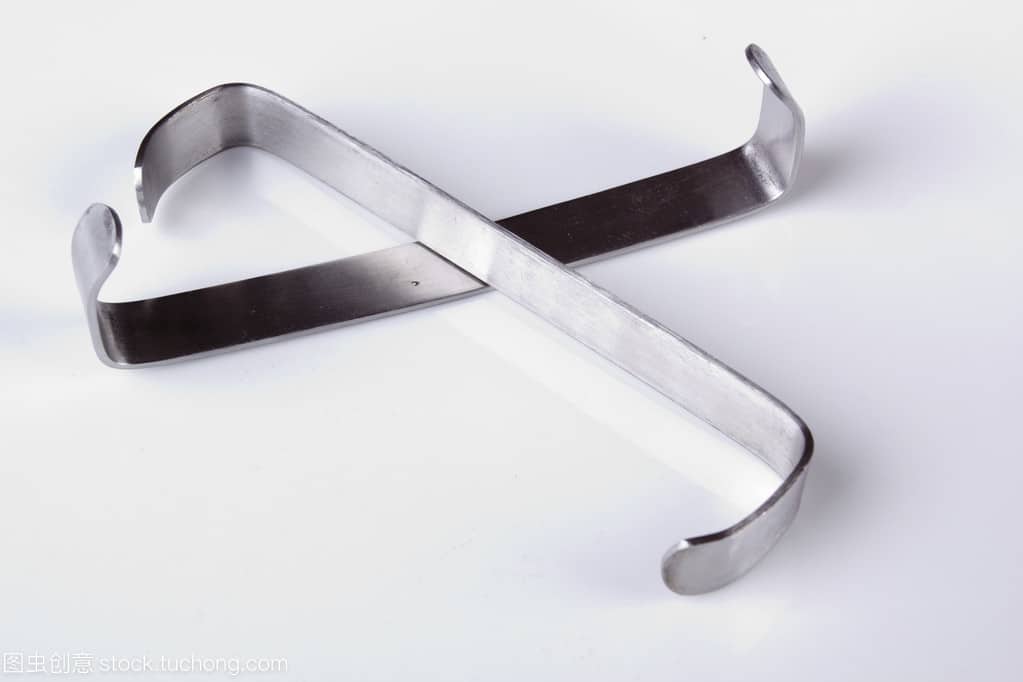
It is difficult to produce this kind of stainless steel claw with complex shape by casting or machining. It requires a long production cycle and high cost. Using metal powder metallurgy technology to produce this kind of claw can save 60% of the cost.
One-off surgical tools need to develop a low-cost batch production process. Smith Metal Products Corporation uses metal powder metallurgy technology to produce a shaft assembly, which can be used in a new type of disposable surgical instruments. The cost is only 1/4-1/5 of that processed by Swiss CNC machine tools, and the density is 7.5. G/cm3, the ultimate tensile strength is 1190 MPa, the yield strength is 1090 MPa, the elongation is 6.0%, and the maximum hardness is 33 HRC.
The manufacturing process of the product is as follows: firstly, two 178mm long axle parts are formed by metal powder metallurgy technology, then two parts are welded by laser, followed by subsequent machining and heat treatment. Sandblasting and passivation are also needed to achieve better tolerance requirements.
Knee implant parts
Metal powder metallurgy technology is progressing slowly in the field of human body implantation, mainly because the certification and acceptance of products need a long period.
At present, metal powder metallurgy technology can be used to produce parts that can partly replace bones and joints. Ti alloy is the main metal material used.
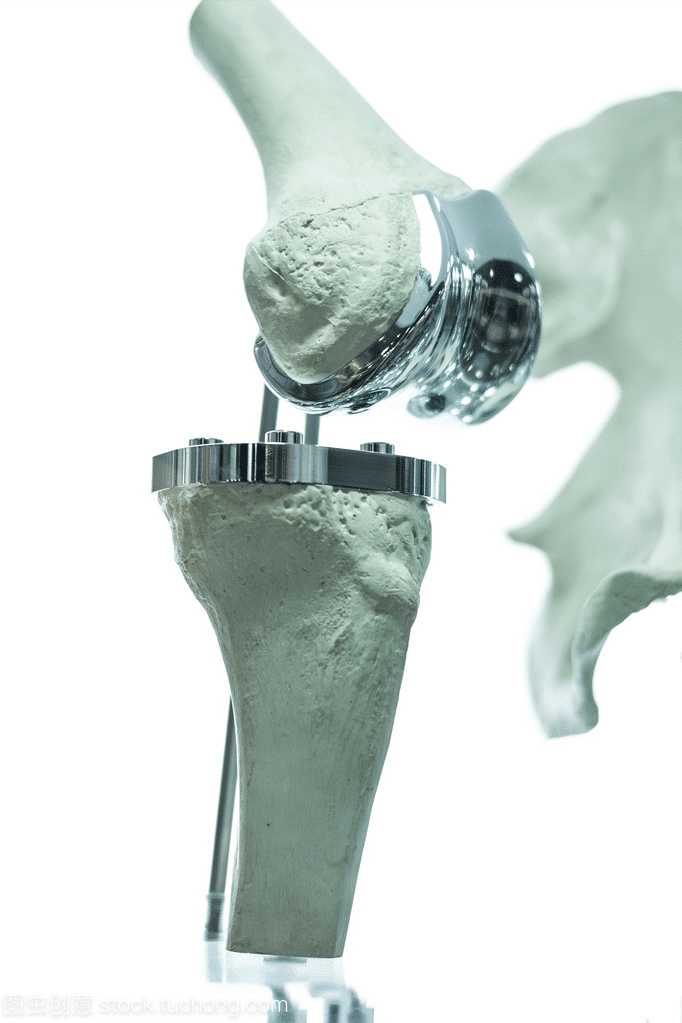
Maetta Sciences Inc of Canada has successfully used Ti-6Al-4V to produce knee sample parts for human body implantation. The implant is mainly under pressure after entering the human body and has good biocompatibility. Metal powder metallurgy is used to form and then hot isostatic pressing, followed by sandblasting, polishing and anodizing to obtain better surface properties, reduce friction with a human body, improve compatibility and service life.
Hearing Aid Sound Tube
Metal powder metallurgy technology can also be used to produce various parts of medical equipment.
Indo-metal powder metallurgy company uses metal powder metallurgy technology to produce a hearing aid sound tube for Phonak company in Germany, which has the effect of improving the sound rate and promoting hearing.
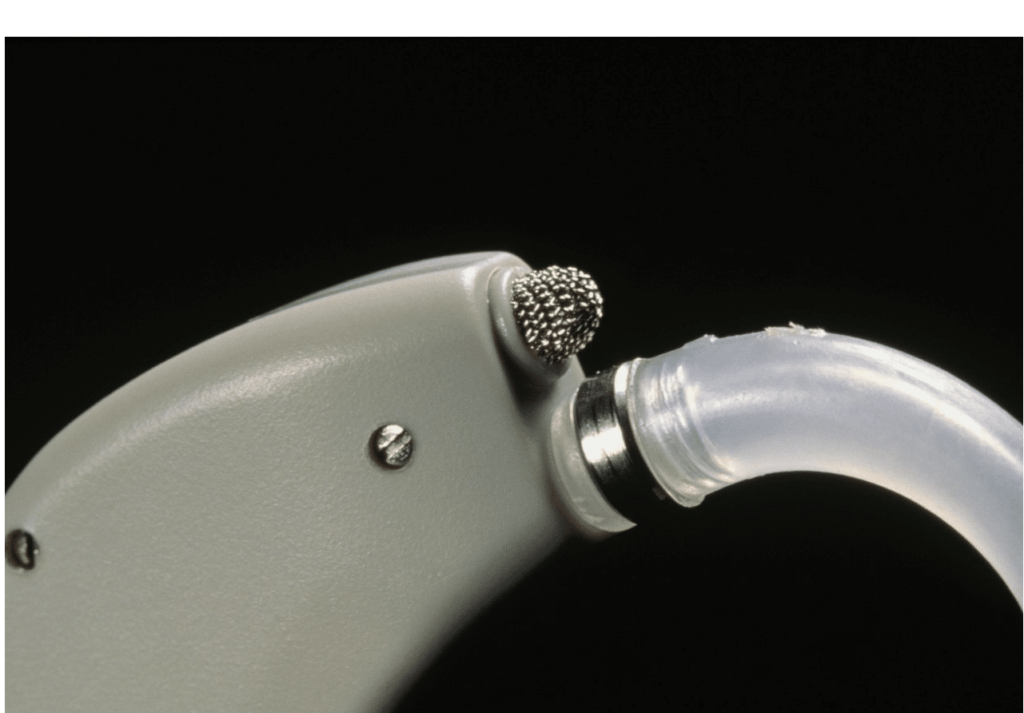
This kind of hearing aid sound tube with complex shape can be obtained by sintering after metal powder metallurgy forming. In order to make the surface of the sound tube smooth, only one glass bead sandblasting process can be followed.
The density of the sound tube is more than 7.65 g/cm3, the maximum tensile strength is 480 MPa, the yield strength is 150 MPa, the elongation is 45%, and the maximum surface hardness is 100 HRB. Metal powder metallurgy technology can reduce the cost by 20% compared with the traditional production process. –
Metal powder metallurgy technology can also be used to produce many medical products, including interventional stents, radiation shielding of tungsten high-density alloy syringes, microsurgical manipulators, micro-pump endoscope parts and drug inhalers. –
Prospects
According to BCCresearch’s recent market research on metal and ceramic powder metallurgy, the global market value of the metal and ceramic powder metallurgy components will increase from $1.5 billion in 2012 to nearly $2.9 billion in 2018, with an average annual growth rate of 11.4%.
At the same time, with the decline of automobile sales, metal powder metallurgy technology will be more into medical, aerospace, electronics and other fields.
In the new version of the European Powder Metallurgy Industry Roadmap, the European Powder Metallurgy Association points out that the medical market is an extremely important part of the powder metallurgy industry.
With the continuous expansion of the market, the application of metal powder metallurgy technology in the medical field will be more and more in-depth. Various new materials and processes based on metal powder metallurgy technology will also be constantly developed.